Introduction
Automation has become a real game-changer in today’s fast-paced manufacturing industry. Simply put, it refers to the use of machines, robots, and computer systems to automate industrial processes and tasks, thereby reducing the need for human intervention.
By implementing industrial automation, companies can streamline their operations, reduce production time, minimize errors and defects, and increase throughput. Moreover, it allows companies to produce goods at a lower cost and with greater precision, which ultimately leads to higher profits.
Let’s delve into the technology behind it and explore how it applies to your business.
Components of
Industrial
Automation
Industrial automation involves a complex framework of components that work together seamlessly to ensure optimal performance.
- Programmable Logic Controllers (PLCs) are at the heart of industrial automation. These devices are essentially mini-computers that are programmed to check the actions of machinery and equipment. They use a combination of hardware and software to monitor inputs, data and generate outputs, all in real time. PLCs are incredibly versatile and can be programmed to perform a wide range of tasks, from simple on/off switching to complex calculations and logic operations.
- Human Machine Interface (HMI) is the component that allows operators to interact with the automation system. HMIs typically consist of a touchscreen display that displays real-time data from the system and provides access to controls and settings. They allow operators to monitor performance, diagnose problems, and make adjustments as needed. HMIs are crucial for ensuring that the network is operating correctly.
- Supervisory Control and Data Acquisition (SCADA) systems are utilized to monitor and adjust large-scale industrial operations. These systems typically consist of a network of sensors, PLCs, and HMIs that work together to collect and analyze data from the procedure. SCADA can help monitor a wide range of processes, from power plants and water treatment facilities to manufacturing plants and transportation. They allow operators to make real-time adjustments, ensuring that everything runs smoothly.
- Distributed Control Systems (DCS) are similar to SCADA but are typically used to regulate smaller-scale stages. DCS consists of a network of controllers and sensors that combine to oversee each step. They are designed to provide precise supervision over individual variables, such as temperature, pressure, and flow rate. Industries often working with DCS include food and beverage, pharmaceuticals, and oil and gas.
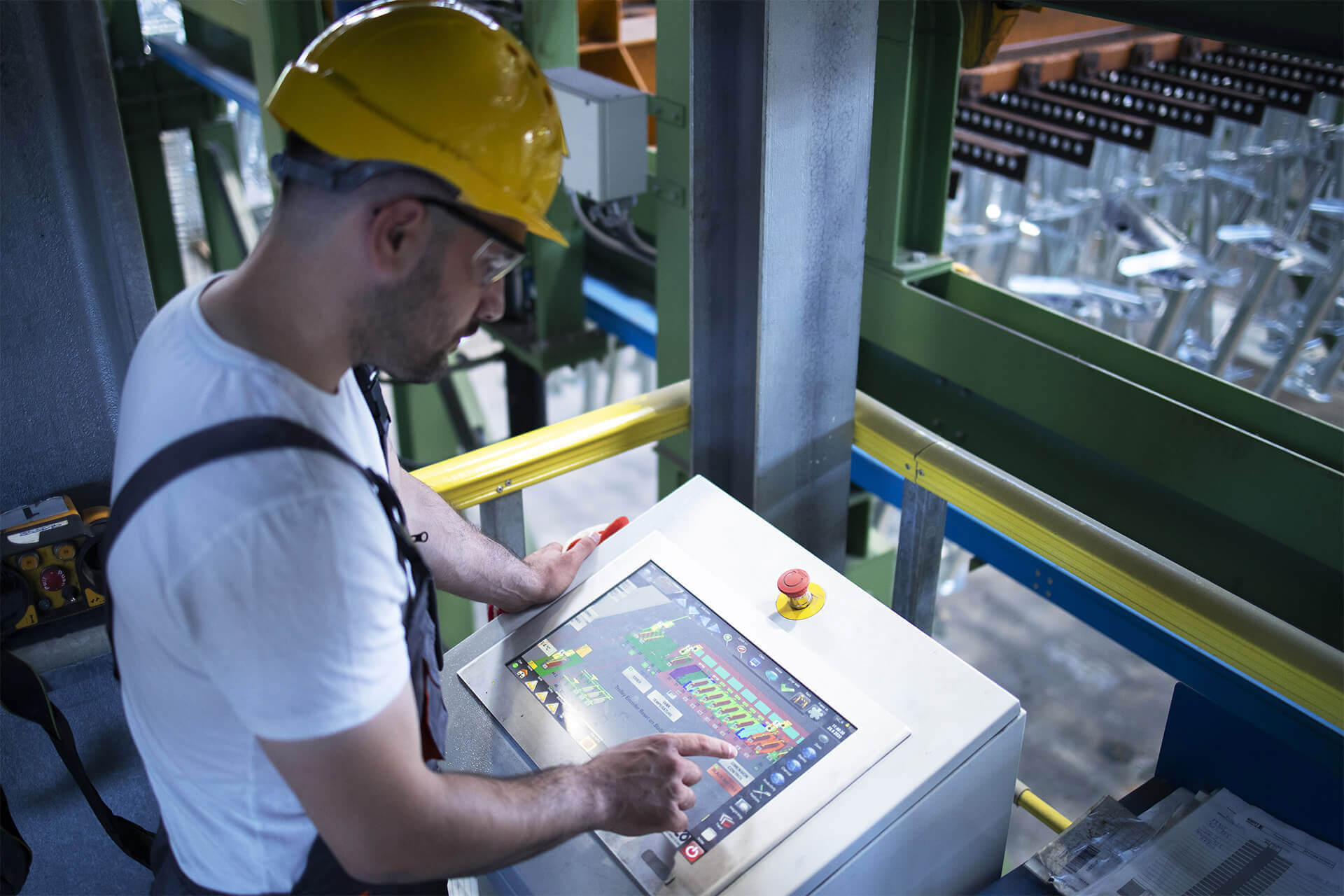
Industrial Automation
processes
Industrial Automation processes
Diving deeper into the operations within industrial automation, here are some of the paramount processes:
Control systems
These are used to regulate and optimize the performance of machines and equipment on the manufacturing floor. Ranging from simple on/off controls to complex algorithms, they adjust machine performance based on real-time data.
Robotics
Increasingly employed in manufacturing to automate repetitive and physically demanding objectives, industrial robots can perform a wide range of tasks, from welding and painting to assembly and packaging. Robots are also becoming more sophisticated and are able to learn from their environment and adapt to changing conditions.
Machine vision systems
Helpful when it comes to inspecting and analyzing products as they move along the manufacturing line, these systems use cameras and image processing software to identify defects, measure dimensions, and ensure that products meet quality standards.
AI
Optimization of manufacturing workings and improvement of quality control: machine learning algorithms can analyze large amounts of data to identify patterns. As a result, they predict maintenance needs and reduce downtime by identifying potential issues before they cause problems.
By leveraging these technologies and systems, manufacturers are able to produce goods faster, more effectively, and with a higher level of quality than ever before.
Applications
Now to the burning questions: what are practical industrial automation solutions for manufacturers?
Area | Manufacturing | Assembly Lines | Quality Control and inspection | Material handling | Packaging and shipping |
Industrial automation allows you to | Upgrade the entire manufacturing process. From raw materials to finished products, each step is completed dynamically and accurately. | Regulate the movement of products along the assembly line, including everything from regulating the speed of conveyor belts to guiding robotic arms that perform assembly tasks. | Inspect and analyze products to ensure they meet quality standards: measuring product dimensions, identifying defects and anomalies, and much more. | Move raw materials and finished products throughout the manufacturing process, like loading and unloading materials to transporting products from one machine to another. | Package and ship finished products: from filling containers with products to labeling and preparing them for shipment. |
Conclusion
Industrial automation has transformed the manufacturing landscape, making it more efficient, productive, and profitable. By embracing this technology, manufacturers can stay ahead of the competition and continue to deliver exceptional goods to consumers. With PLCs, HMIs, SCADA, DCS, robotics, machine vision systems, and AI at their disposal, the sky’s the limit for what to achieve in modern manufacturing. The world has entered a new era of production, where humans can focus on innovation and creativity while machines take care of repetitive and mundane tasks.
If you are ready to learn more about how industrial automation can help your business, get in touch with SIA today! Our team of experienced professionals will work with you every step of the way to ensure that solutions are tailored to your specific needs and requirements.
Don’t just take our word for it, check out our case study here. We have partnered with a global leader in tobacco production. Through integrating SCADA with ERP systems and providing them with a single source of data truth throughout their entire manufacturing process, we managed to improve efficiency, increase transparency, and accelerate data availability and synchronization.