Introduction
Industry 4.0 is undeniably a buzzword right now. First things first, what does it really mean? We have seen claims that it transforms manufacturing, but how exactly? And most importantly, what are the Industry 4.0 business opportunities for your company specifically?
Industry 4.0, or the fourth revolution, paves the way for ‘smart’ systems and digital integration. Taking over almost every industry around the globe, it is associated above all with the digitization of the manufacturing sector: ubiquitous cyber-physical systems with sensors embedded in practically every product component and equipment, constantly accumulating and analyzing data.
Industry 4.0
in Manufacturing
When applied to the manufacturing industry, Industry 4.0 is the integration of smart manufacturing machinery, AI-powered automation technology, and advanced analytics to decrease costs and heighten efficiency on every level of production and the supply chain: inside their factories, warehouses, workshops, and between them. This revolution enables receiving and processing of far greater amounts of info faster and more effectively than ever before.
It is powered by 4 clusters of disruptive technologies. Data, computational power, and connectivity are the first, one of the main goals being to set up a low-power, wide-area network. The second of so-called pillars is analytics and intelligence. Human-machine interaction is the third, and digital-to-physical conversion is the fourth, striving to utilize tech like advanced robotics or 3D printing to their full potential.
Industry 4.0
in Logistics
From warehouse operation management to transportation along the supply chain and up to the sale points, Logistics is an integral part of manufacturing. To meet demand of the modern sector, an intelligent, fully automated, and progressively autonomous flow of assets, goods, materials, and information between the origin point and the consumption point, and the numerous points in-between — is critical.
End-to-end information chains are no longer sufficient, so there is a need for smart master data maintenance. It entails upgrading the use of smart labeling, ICT, GPRS and 3G modems, RFID, combining them with low power networks (which allow to sensor the pallets), web browsers or apps. This results in pick-by-voice, pick-by-light, or pick-by-scan solutions, as well as AI-based systems, fit for quality assurance and warehousing; optimization of routes that relies not only on its own historical facts but also current information from external sources, such as traffic conditions.
It’s time to upgrade from data and autonomous decision-making to intelligence and actions.
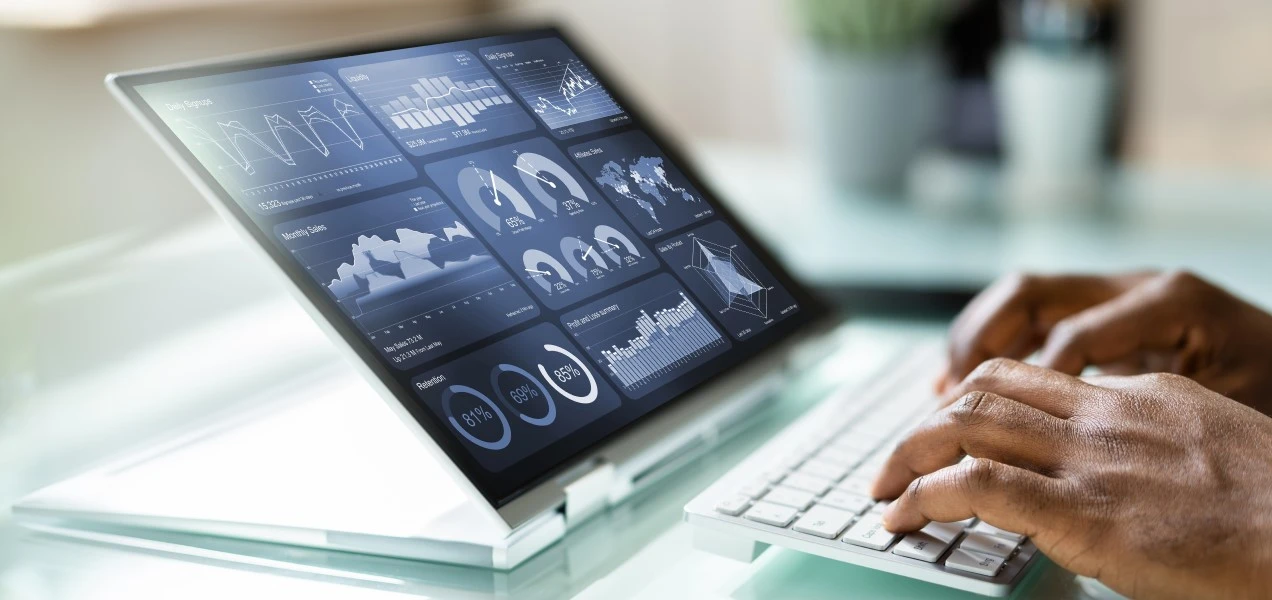
Industry 3.0
vs. Industry 4.0
A prominent example of the ‘old’ way is a CNC machine: although it is predominantly automated, it still needs a human operator. Process automation is built upon human input, not data. That is where Industry 4.0 transcends 3.0: that same CNC machine is able to not only follow set programming parameters but also collect and analyze input to streamline production processes.
The principal difference between the two is rather ideological. The new age adopts existing technologies and then combines them in new, innovative ways. Thus, in contrast with the Industrial revolutions before, the fourth one does not aim to substitute existing assets with new ones but rather strives to tackle the managerial challenges posed by market disruptions. Every transaction leaves a digital footprint, so the system can trace the whole process. Precisely due to tracking and extracting info, there is an opportunity to analyze and regulate the whole system.
Lean production has to transform into smart production. Now, smart factories gain the ability to predict failures before they happen and propose a solution autonomously, which may prove to be a critical competitive advantage. This digital transformation forces the workforce to upskill themselves to these new realities and job roles.
How to implement
Industry 4.0 technologies?
Technology matters! Let’s look at how different technologies can be applied to accelerate your business.
IoT in Industry 4.0
IoT comprises devices and machinery connected by communication machinery, all to relieve companies from collecting, analyzing, and acting upon reports. It transforms existing legacy infrastructures within industrial and manufacturing processes, with opportunities for automation in factories, process optimization, intelligent manufacturing, and performance monitoring. The benefits of using IoT in Manufacturing Execution Systems include increased efficiency, predictive maintenance, real-time monitoring, and reduced costs.
Big Data in Industry 4.0
Industrial production of data is gargantuan, and as a result, provides the basis for analysis and vital information extraction. Info collected and created through the processes could be collected and utilized as raw materials for analytics. The field of application of this is endless: production, supply chain, and sustainability can be manipulated to reach higher efficiency levels and promote your business profitability. After-sales operations could be very specialized and extend the product life cycle. Moreover, Big Data can assist in determining future trends in sales and client needs, which is invaluable information for marketing strategies.
Cloud Computing in Industry 4.0
Essentially the foundation of Industry 4.0, cloud computing applications streamline operational and management processes by centralizing data storage, bandwidth, and processing. Users can access the system from the Cloud anytime and anywhere, enabling a real-time exchange of information and creating a comfortable environment for collaboration and integration.
Contrary to popular belief, it is actually a better infrastructure security solution. In addition to higher reliability, it reduces the costs of maintaining a local server and encourages scalability. Last but not least, it allows a proactive management approach.
Robotics in Industry 4.0
Robotics is a fool-proof way to accelerate your productivity. By combining it with AI, companies can enhance human-robot collaboration: improve human safety on the shop floor, give robots more responsibility, even let them make decisions that can further optimize operations. These decisions will be based on real-time info gathered from the production floor.
Do not worry because the Terminator future is not coming. Human workers will not be replaced. The International Federation of Robotics supposes that less than 10% of jobs could be fully automated. Robots are to help with repetitive tasks, allowing human “colleagues” to focus on demanding tasks.
AI in Industry 4.0
AI (Artificial intelligence) revolutionizes automation by bringing human-like levels of understanding to software, lowering the overhead costs and reducing human errors. Its applications can be divided into 5 main categories. AI + Robotics collaboration is mentioned above. The most well-known use of AI is for predictive maintenance to foresee downtime and schedule maintenance procedures so as not to waste time. AI + Machine Learning: using ML algorithms that are uniquely trained to understand each production process, AI can detect and report hidden causes of everyday perennial production losses. AI can also aid in generative design. Finally, AI is used to optimize the supply chain and estimate market demand.
ML in Industry 4.0
ML (Machine learning) opens the possibility of actionable intelligence. Predictive insights form a support system for a wide range of tasks: predictive maintenance, quality improvement, process optimization, intelligent and continuous inspection, task scheduling, and manufacturing operations management. Integrating systems within the factory to be compatible with ML is what makes a ‘smart’ factory. The beauty of ML is that it elevates efficiency without significantly altering existing resources.
Blockchain in Industry 4.0
Incorporating Blockchain can positively impact security, privacy, and transparency for both large enterprises and small businesses. Manufacturers can use blockchain’s features to fix technical challenges and make communication and accountability easier. Smart contracts have many advantages as they allow business operations to begin automatically.
Blockchain is a way to cut expenses and time for the logistics and transportation sectors, becoming a new method of tracking any product shipment or transaction or tracking performance across the product life cycle.
Conclusion
Industry 4.0 has indeed reconstructed how we perceive things in the production units. To stay afloat and push forward, manufacturing and logistics companies should decide how to leverage it to their advantage. Otherwise, they will quickly stagnate and be left behind. The market is a race, and standing still is moving backward.
At Soft Industry Alliance (SIA), we firmly believe that Industry 4.0 is not a threat but an opportunity. However, there is still a question of how to approach such a monumental digital transformation. Unfortunately, there is no cookie-cutter solution, no singular, standardized approach to applying the fourth revolution throughout an organization. This article has laid out possible applications of disruptive technologies, but which to start with and how to combine them for the best results for your specific case?
Here, our SIA team can bolster you. Our automation of manufacturing and logistics specialists will reinforce your team in finding your own solution without needless experiments and wasted budgets. First, we will determine the value drivers that impact the company performance the most. Then we will identify ways to optimize and boost your efficiency to the maximum possible.
Let’s discuss your project! Leave your details, and we will contact you shortly.